Seguimos con la construcción y detalle de mi nueva impresora virtual pero en este y el capitulo siguiente (que probablemente sea el final) me voy a centrar en algunos de los detalles que la hacen un poco especial.
LA IMPRESIÓN A TODO COLOR O CASI CICLO DE PRE-EXTRUSIÓN
En este momento para imprimir en más de un color nos vemos obligados a disponer de n-extrusores, tantos como los colores que deseamos imprimir, lo cual suele acabar en dos colores. Estamos en la televisión en blanco y negro, azul y rojo, etc. , o similar. La solución es crear un hilo multicolor a medida del trabajo a imprimir, esto nos permite, dentro de las lógicas limitaciones de la mezcla de color en la fusión del plástico, realizar trabajos con características de policromía que antes eran inviables.
Técnicamente no es complicado, mejor dicho es posible, cuando laminamos nuestro trabajo ya calculamos los metros de plástico que necesitamos y en caso de usar varios colores alternamos en el momento exacto el uso de uno u otro extrusor. Ahora solo hay que trasladar este cálculo al pre-extrusor contando con el retardo necesario para que se introduzcan los nódulos del color deseado, se extruyan y lleguen al extrusor final en su momento. Un poco mas de calibración y matemáticas básicas.
Luego tenemos estrategias de impresión para la zona impura de inicio de un nuevo color, habrá que estudiar su inclusión en zonas de relleno o depositar una cierta cantidad fuera de la zona de impresión , incluso cierta programación manual para determinar cuándo empezar a imprimir con el color nuevo.
Para el cambio de tipo de material o incluso para selecciones particulares de colores la tolva debe ser un elemento que podamos imprimirnos de forma que nos permita tener varios modelos y combinaciones. Porque quien nos quita en un momento dado trabajas con material imitación madera y plateados para maquetas arquitectónicas, combinar distintos materiales por características o flexibilidad para piezas con funciones especiales, eso sí con una labor de programación, combinación de temperaturas y otros factores que nos obligaran casi al virtuosismo.
Claro también esto producirá siempre un excedente entre pieza y pieza que porque no usarlo para la elaboración de repuestos de nuestra maquina o piezas para el banco de piezas de la comunidad. O bien parar esos sobrantes a los procesos de reciclado que hayamos establecido de forma personal o quizás por economía de escala de forma colectiva entre todo el grupo local.

ALGUNOS DE SUS COMPONENTES
El primer extrusor va a convertir el granulo de material en el filamento que usaremos para la extrusión de la pieza,
En primer lugar estará la tolva de material la cual estará dispuesta en compartimentos que albergaran los distintos colores o materiales según la impresión que vallamos a realizar. Como dijimos antes será de material impreso por nuestra maquina y existirán varios modelo es de uno hasta cinco o seis compartimentos independientes los cuales dejaran caer el material por gravedad ante la apertura de las trampillas inferiores deslizantes que controlaran que color y durante cuánto tiempo llegara al impulsor.
El impulsor es un tornillo de Arquímedes que girara por medio de un motor reductor e impulsara estos nódulos hacia la zona del extrusor propiamente dicho, el cual estará incrustado dentro de un tubo metálico y recibirá la aportación de material desde una abertura superior en el tubo.
El hot-end propiamente dicho se compone de una barrera térmica en principio de tipo cerámico y con un interior cónico que pasa de 30 mm a 15 en la zona de fusión y que mantendría el empuje que se realiza desde el tornillo, a continuación estaría la zona caliente en cobre o bronce y donde se aporta temperatura y que mantiene la forma cónica de 15 a 9 mm y por fin la cabeza extrusora también de bronce con perfil cónico de 9 a 2.92 mm de salida aprovechado la situación más liquida del material.
En el momento de la salida de este material se procede a un enfriamiento rápido y paulatino por medio de ventilación y disipadores de forma que podamos manejar el hilo y llegue en unas condiciones de dureza para el empuje del extrusor de impresión y su correcta conducción por un tubo boden hasta el hot-end de impresión.
Tanto la disipación de calor del extrusor como del enfriamiento del hilo se reconducirá hacia la zona de impresión para climatizar esta zona.
En este apartado necesitaremos un motor reductor para mover el tornillo de impulsión del material, cinco o seis servomotores pequeños para las aperturas de la tolvas, un calentador y su termistor para la extrusión del material y de 2 a 4 ventiladores para los enfriamientos y la conducción térmica.
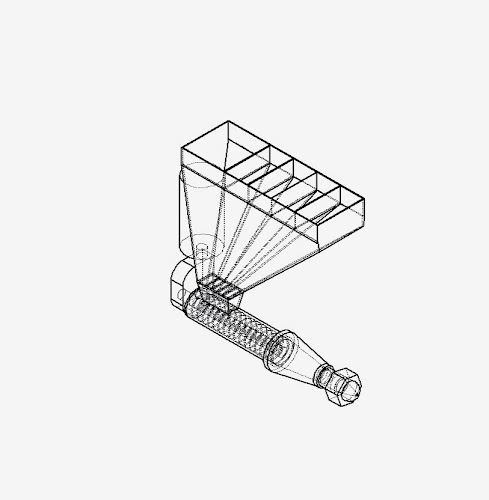
La placa de control un arduino uno controlado por las señales de la placa principal y un grupo de relés para los accionamientos del motor reductor y los ventiladores completarían esta parte de mi nueva impresora.
Y el resto para el próximo capítulo
No hay comentarios:
Publicar un comentario